The brief
Our customer is a private company that produces high-efficiency heat pumps for private households and industrial facilities.
He described the following issues:
- In about half of the cases when the technical support team goes to the end user’s site, no hardware faults are found; changing the pump’s operating parameters is enough to eliminate anomalies in cases of this kind. The number of such trips should be minimized to save time and money.
- Customer`s end users provided negative feedback regarding the pump control interface. Since the equipment is controlled from the built-in display, it is necessary to come to the technical room every time to change the operating mode.
- Collecting telemetry and debugging the operation of the pump requires a physical connection to the pump control board, which requires a physical presence near the pump.
Challenge
The main challenge was to find a versatile and efficient way of solving the presented tasks all at once, without addressing each problem individually.
Solution
We developed the firmware for the microcontroller of industrial heat pumps to connect them to the cloud platform, enabling remote control, monitoring, and configuring features for the manufacturer and end-users.
Since the ESP32 MCU controls the customer’s equipment, we proposed to modify the existing firmware to be compatible with the 2Smart Cloud cloud platform. Such an approach allowed us to solve the presented problems in the short term without breaking the bank.
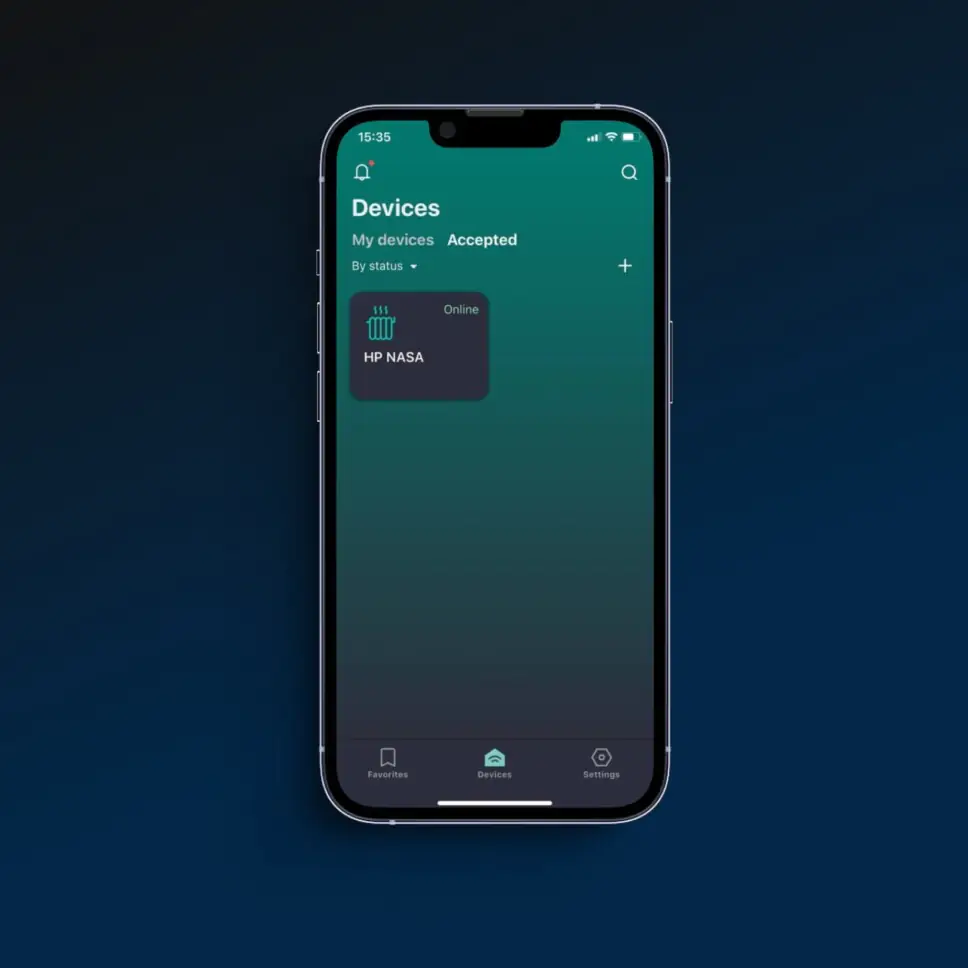
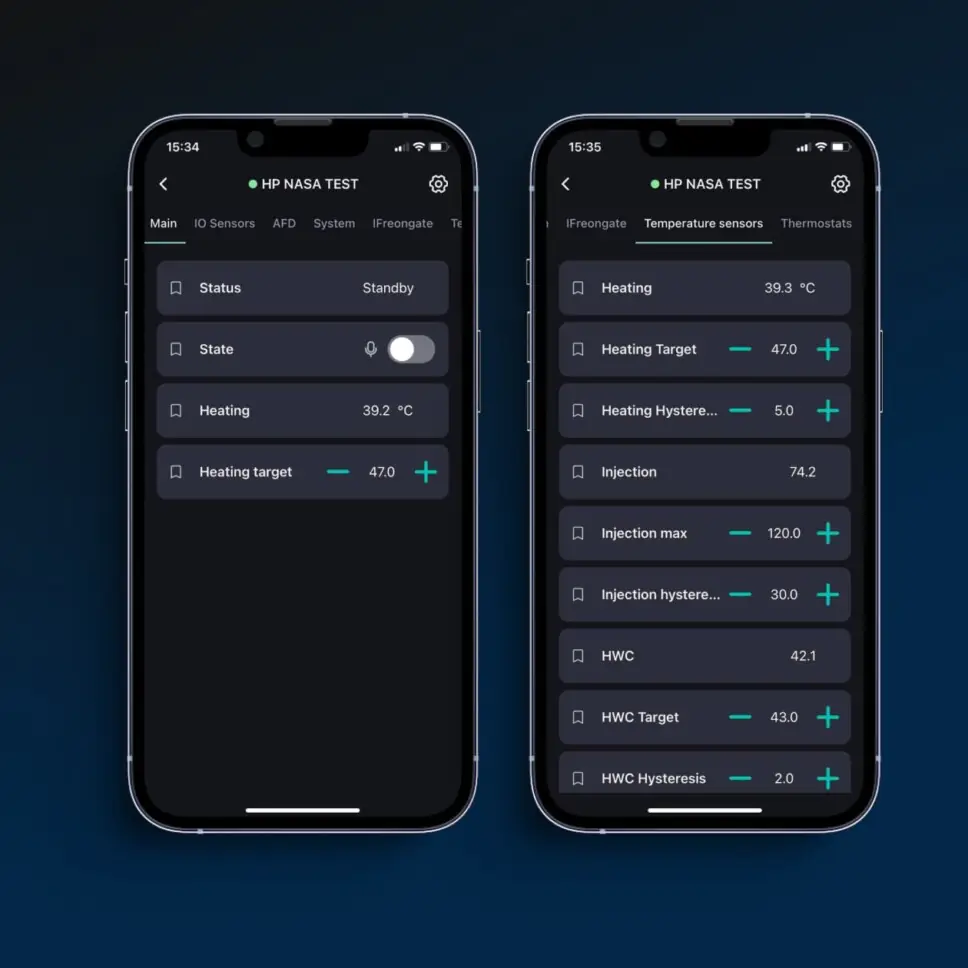
Key features
After changing the firmware for industrial heat pump equipment, the customer received:
- Cloud-based storage of historical data of the operating parameters of the pump, which allows remotely diagnosing the problem, as well as a remote configuration tool to reduce technical support on-site visits;
- Modern and functional mobile application to remotely control the pumps for end-users ;
- A tool for remote collection and analysis of telemetry via a web interface;
Results
Cut post-sales support costs by 30% by reducing technical team on-site visits.
According to surveys, the average end-users grade for pumps has increased from 7.3 to 8.0. Overall, NPS rose from +54 to +59.
Thanks to remote telemetry collection, analysis, and configuration tools, it was possible to increase the overall energy efficiency of already operating pumps by an average of 4.35%.